Ultra-effective shields against pressing water.
When does pressing water become a problem?
Pressing water always becomes a problem if the vertical wall seal is either not present or is not working effectively. in the best case scenario the outer wall affected can be exposed and sealed accordingly. Where excavation work is not possible or only possible at extreme financial cost, depending on the circumstances mibag recommends masonry or curtain injection from inside.
Masonry gel injection
Pressing water infiltrates the masonry through small fissures or cavities. In the masonry gel injection process the major weak spots are blocked on the outer part of the wall. For this, the injection substance is injected in under pressure via bore holes that penetrate the outer third of the wall. The gel thus inserted reacts with the damp there, binding this to create a hydrophobic barrier lock. This technology is most often used on mixed masonry structures.
To regulate the moisture balance in the wall, the existing plaster must be chipped off and replaced with a breathable damp wall plaster.
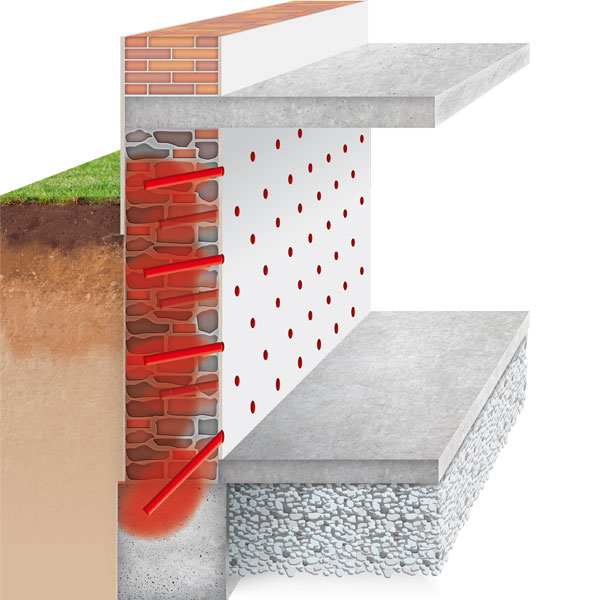
Masonry gel injection: the significant weak points in the masonry are filled with pressure-injected acrylate gel.
Curtain injection
If the masonry displays especially large cavities (e.g. filling bricks), in many cases it is more economical to seal not the masonry itself but rather the area in front of the wall. Use of injection agents is therefore dependent on the composition of the backfill material adjacent to the wall. With curtain injection, the injection agent is pumped through the pre-drilled bore holes in front of the masonry. The waterproof gel layer builds up in front of the building structure and ensures lasting protection.
The acrylate gel used is utilised for both curtain injection and masonry injection. It poses no physiological risk and is completely harmless in all applications affecting groundwater.
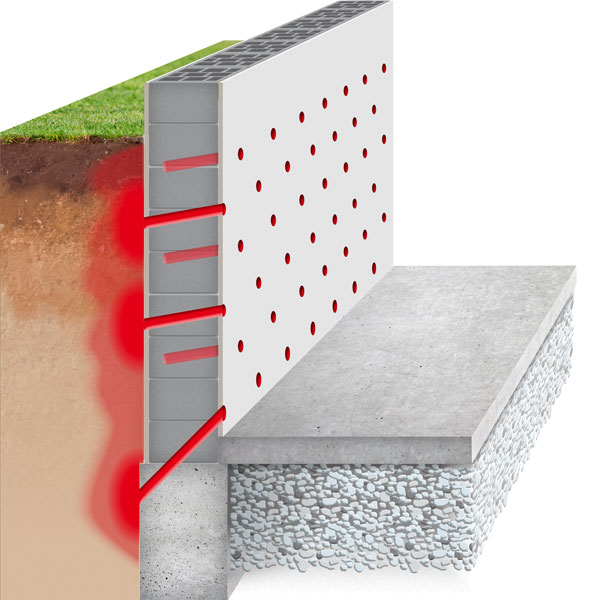
Curtain injection: the acrylate gel is pumped not inside but in front of the masonry.
Sealing joints
Construction joints appear in concrete structures that are constructed in multiple sections. Missing or defective joint tapes or seals cause water ingress and, consequently, damage to the structure. Construction joints are pierced through at regular intervals to seal them. The joints are then grouted with the appropriate injection agent using steel packers. The pneumatic, multi-component piston pumps work at a pressure of up to 250 bar. Depending on requirements, microfoams, PU or epoxy resins may be used.
Movement or expansion joints are located between building elements and are consciously planned in to avoid stress cracks occurring later on. Depending on the circumstances, restoration is carried out by means of pressure injection using expandable, swellable injection rubber, or elastic joint tapes in combination with epoxy resins.
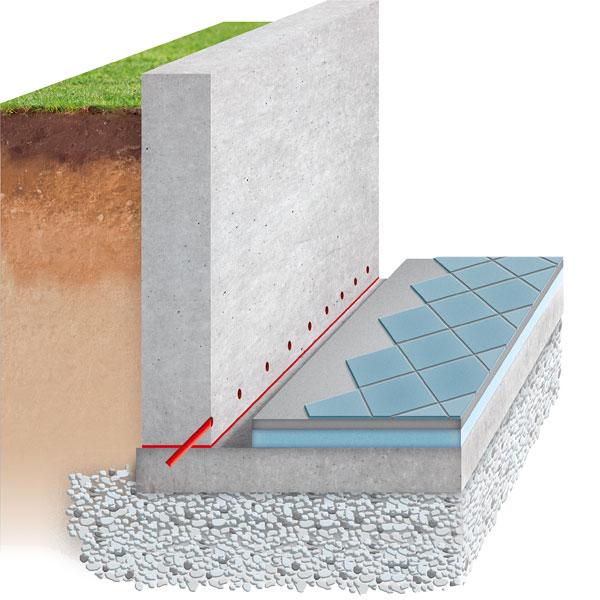
Rising joints: the joints are first bored and then grouted at a pressure of up to 250 bar.
Fissure grouting
Fissures appear due to fluctuations in temperature, building defects or subsidence. Corrosive substances (such as water) can infiltrate these unsealed areas in buildings. Apart from the unwelcome dampness, this can also reduce the load-bearing capacity of the affected walls. The process of sealing via grouting the fissures functions in a very similar way to sealing joints.
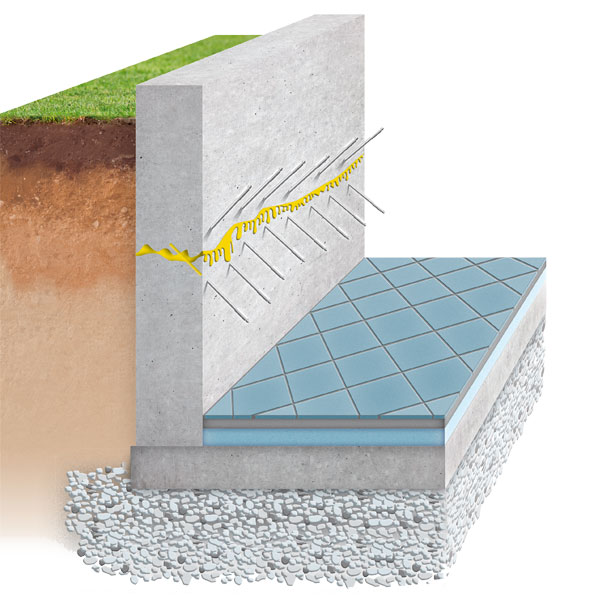
Efficient: fissures are blocked off from the inside using the appropriate injection agent injected under pressure. The injection bore holes required are arranged in a grid system.
-
Cavity filling
-
Sealing pipe penetrations
-
Surface damp-proofing using cement or epoxy resin